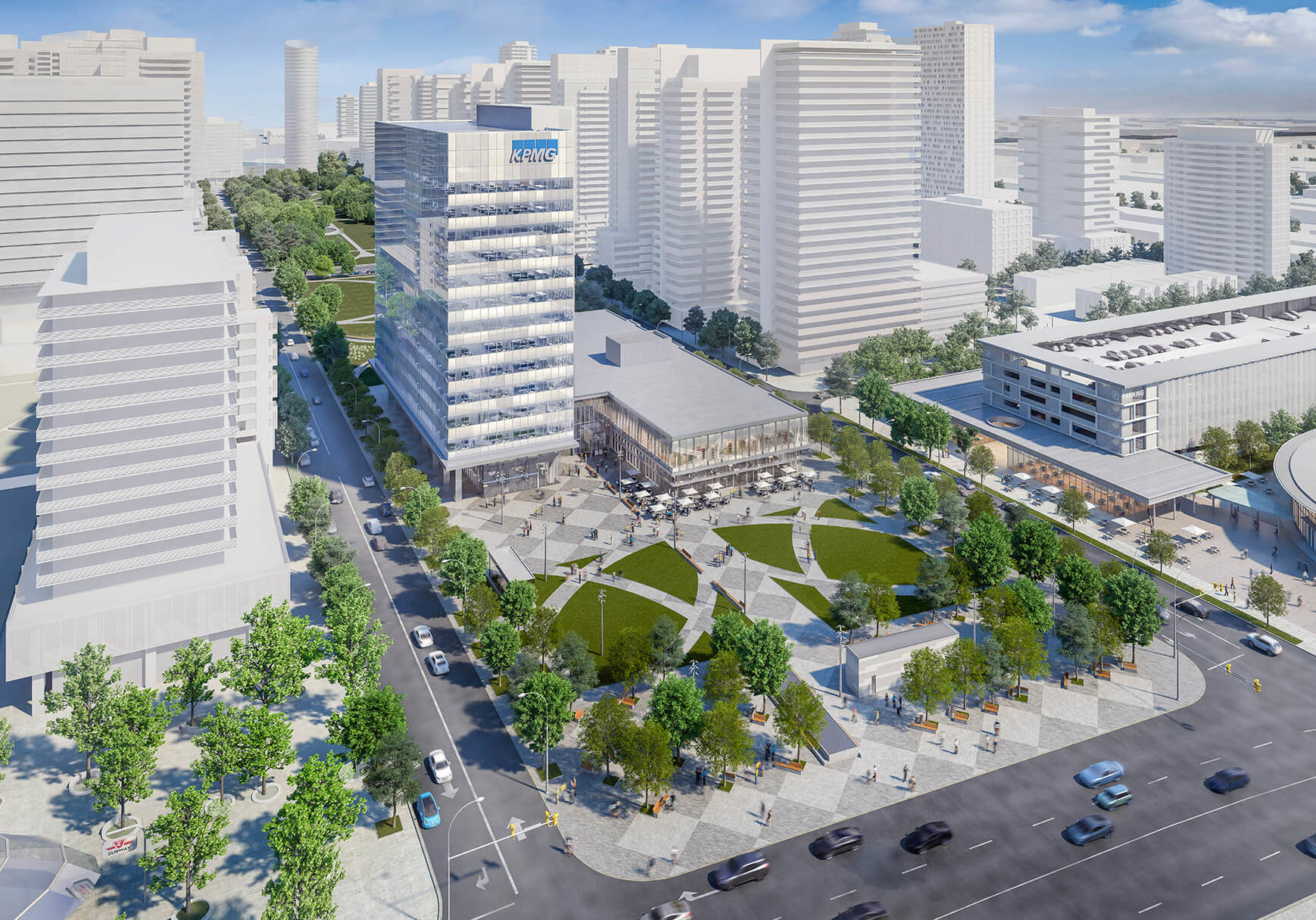
KPMG Tower Vaughan Metro Centre
PROJECT DESCRIPTION
The Vaughan Metropolitan Centre (VMC) is an emerging urban core within the Greater Toronto Area. This 400-acre planned downtown for the City of Vaughan provides all the amenities of a vibrant city centre including direct access to a multi-modal public transit hub.
The first development within the VMC was the KPMG Tower—a 15-storey, 365,000 sq. ft. targeted LEED Gold core and shell office building with ground floor retail and an additional 2-storey retail wing. The facility also has surface parking, an exterior civic plaza, and two levels of underground parking connected to the adjacent new Toronto Transit Commission subway station, surface parking and an exterior civic plaza/square.
B&M SCOPE OF WORK
Black & McDonald (B&M) was responsible for the supply, installation and commissioning of all mechanical services: a plumbing system including installation of incoming water line backflow preventers; a heating water distribution system; a chilled water distribution system; air handling distribution; humidification systems; a condenser water distribution system; chillers; fire protection and generator fuel system; automatic controls; and instrumentation.
INNOVATIVE PROCESS AND TECHNOLOGY USED
KPMG’s office was pre-constructed in Autodesk Revit to create a dynamic 4D virtual model of the entire building complete with systems and equipment, before and during building construction. Valuable engineering opportunities were realized through review of the model. Mechanical systems including mechanical room pumps, heat exchangers, piping systems for both HVAC piping and plumbing systems and carriers were mounted on skids. Fabrication and installation drawings included Trimble Field Points for layout that were developed to facilitate precise installation of the systems on-site. Pre-fabrication and spooling performed in the controlled environment of the shop further enhanced B&M’s quality assurance process and site safety. The overall building process improved efficiency through a condensed schedule and LEAN construction. There was better utilization of labour and material. For instance, the bulk of packaging materials and associated labour for unpacking, storing and disposal were avoided at site saving time and money. Concurrent construction activities further enhanced logistics and reduced the project schedule. Henceforth, the project team had better clarity in evaluating changes for impacts on benefits and risks, enabling them to make more intelligent and timely decisions, mitigating risks.
In-house fabrication played a critical role in adhering to the fast-track schedule. Wall plumbing rough-in banks for all washrooms as well as 99 percent of all HVAC piping were prefabricated in B&M’s fabrication shop in Scarborough, Ontario.
Related Project Profiles
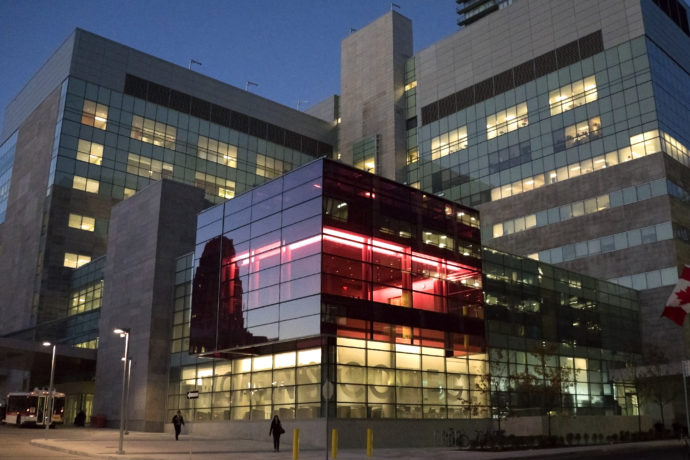
Women’s College Hospital Phase 2
Black & McDonald is part of the P3 consortium to deliver the Women’s College Hospital Redevelopment (WCHR) project which included the financing, design,…

University of Toronto Central Steam Plant
Black & McDonald delivered this Design Build project for the University of Toronto with a goal of reducing the greenhouse gas emissions of…
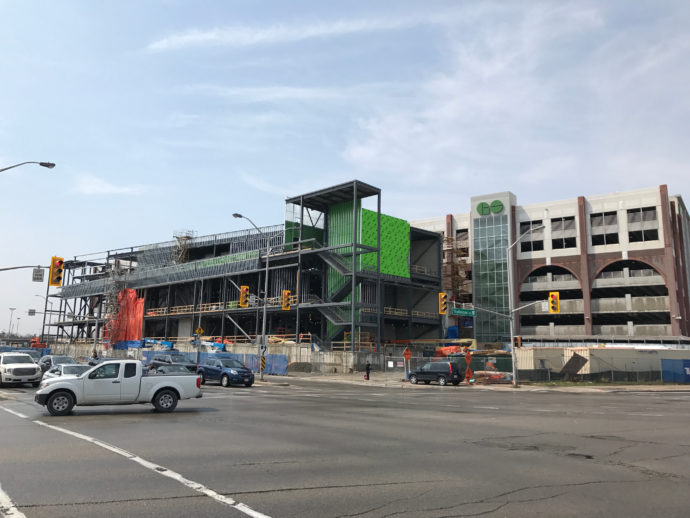
GO Transit Control Centre
Black & McDonald was responsible for all Electrical, Communications, HVAC, and Piping Installation on this new state of the art LEED Gold facility.

North End Water Pollution Control Centre Supply Upgrade
The work included construction of a new switchyard to house redundant 30 MVA transformers, a new electrical building and electrical distribution to feed…
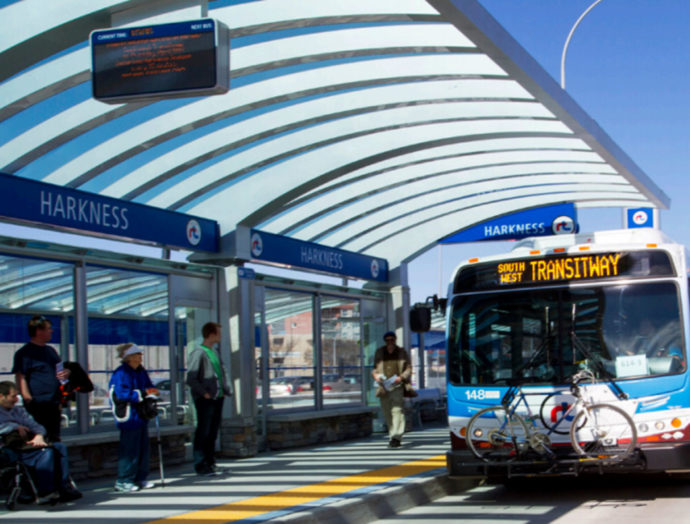
Winnipeg Southwest Rapid Transitway and Pembina Highway Underpass
The project involves the continuation of the dedicated Transitway in Winnipeg from Pembina Highway and Jubilee Avenue to the University of Manitoba, as…

GO Transit Union Station Train Shed Revitalization 65 Front Street West
Black & McDonald contributed to the development of the train shed by providing all project management, supervision, labour, equipment, and materials to deliver…

Union Station Revitalization Integrated Stage 2 and 3
Scope of Work covers all aspects of the final consolidated phase of construction for the The Union Station Revitalization Project (USRP) Integrated Stage…

Toronto Transit Commission Duncan Shop Ventilation Upgrade
Black & McDonald contributed to the development of the train shed by providing all project management, supervision, labour, equipment, and materials to deliver…

Toronto Hydro Electrical Services – Office Fit-out
Black & McDonald was the general contractor providing labour, equipment and materials for installation, testing and commissioning of all systems as well as…

Metrolinx Georgetown South Corridor Track & Signal Construction
The Black & McDonald scope of work includes the supply of materials, labour, equipment, and permits necessary for the upgrade of process control…

City of Winnipeg North End Sewage Treatment Plant Power Supply Upgrade
Black & McDonald performed a complete fit-out of the Toronto Hydro Electrical Services office space and truck fleet garage.

Manitoba Hydro Louis Riel Substation Construction
B&M’s scope of work included supply of all supervision, qualified labour, tools, equipment, hardware and materials required to complete project.

Keswick Water Pollution Control Plant Expansion
Black & McDonald’s scope of work included electrical, instrumentation, PLC and SCADA implementation and commissioning work as part of the plant expansion of…
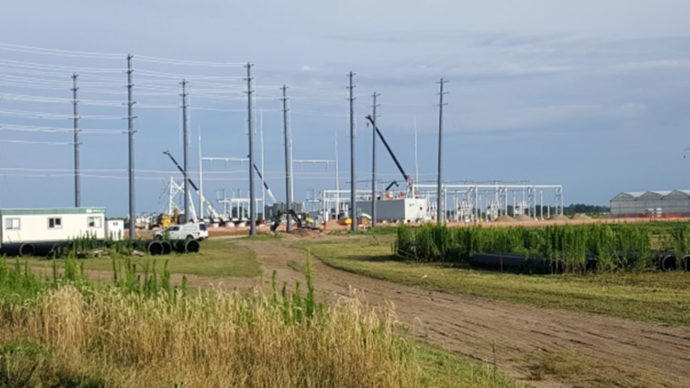
Hydro One Leamington Transfer Station
Black & McDonald was the general contractor during this project. The station was built as the total load in the area exceeds the…

Hydro One Leamington Transformer Station
Black & McDonald was the general contractor during this project. The station was built because the total load in the area exceeds the…
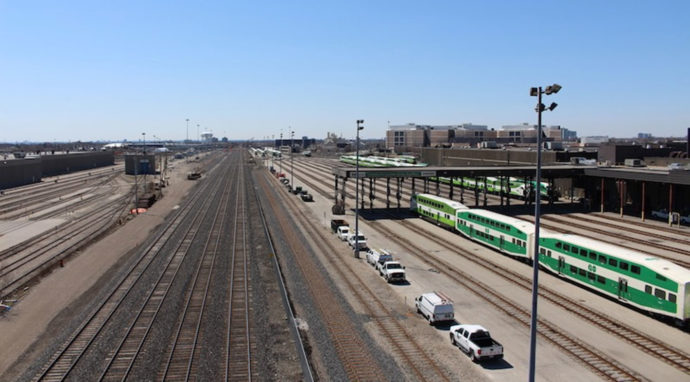
Metrolinx ERMF Mainline Track and Signals East Rail Maintenance Facility
The project included modifying an existing plant, Victoria, and completely relocating another plant, Thickson, allowing the installation of new turnouts into and out…

Pumping Station – Water Pollution Control Plant
The project involved the construction of a new influent pumping station, headworks building, biofilter odour control system, and flow metering building for the…

Humber Wastewater Treatment Plant Odour Control Plant Process Upgrades
Black & McDonald was the building odour control contractor during the construction of two new biofilters (central and south biofilter) to treat air…

City of Toronto Adaptive Project Traffic Signal Control System
As a pre-qualified contactor with the City of Toronto, Black & McDonald was awarded the contract for the design, supply, delivery, implementation and…

Ashbridges Bay WWTP Standby Power Upgrades
Major treatment processes include screening and grit removal, primary treatment, secondary treatment, phosphorus removal, effluent disinfection, waste activated sludge thickening, anaerobic digestion, biosolids…
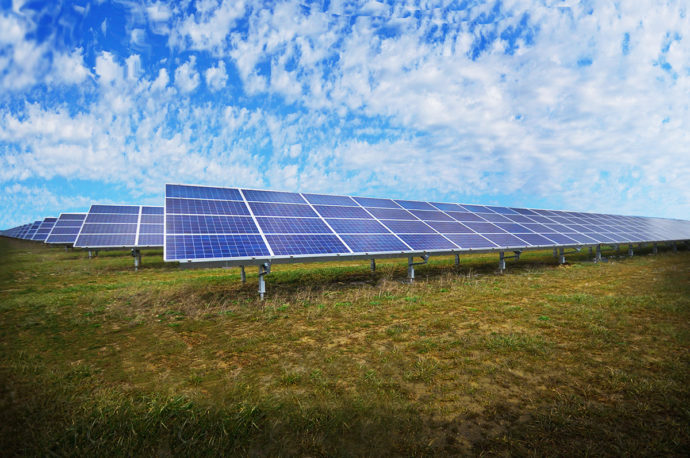
Rainy River First Nations Solar Parks
Black & McDonald was responsible for the complete re-commissioning of the relay protection for the MOT transformer, UST transformer, bus, line differential, breaker…
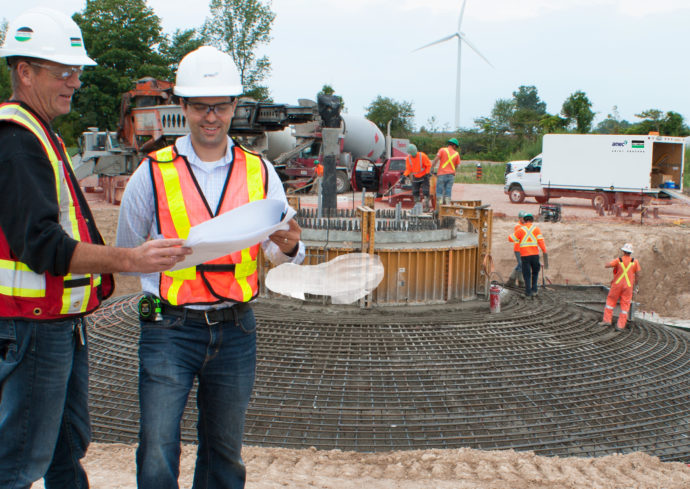
K2 Wind Farm
Together with Black & McDonald’s Joint Venture Partner AMEC, Black & McDonald’s Southern Ontario Utility Region was awarded the engineering, procurement and construction…
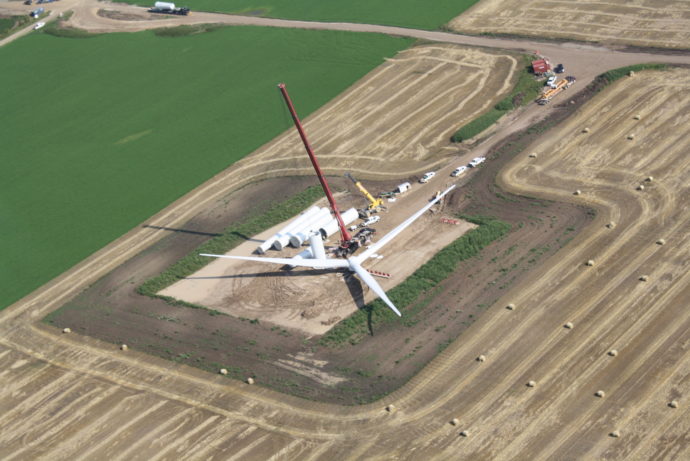
Armow Wind Farm
Services provided by Black & McDonald’s team included installation of a 34.5 kV /230 kV substation, installation of a 230 kV Switching Station,…

Baxter Healthcare CIVA Centre
The project consisted of the construction of a new state-of-the-art facility for Baxter’s Centralized Intravenous Admixing Pharmacy Service (CIVA).

Expansion of the Gaz Métro Plant
Black & McDonald was designated general contractor for the construction of the Linde Process Plants’s Gaz Métro Liquefied Natural Gas (LNG) plant expansion.

Horizon Project VDU/DRU/HSU
Our Black & McDonald Western Canadian Industrial Region was proud to join forces with TR Canada in the oil sands project at CNRL…
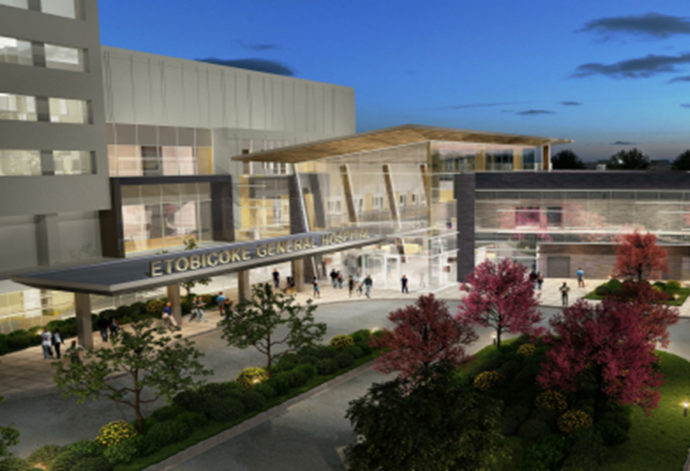
Etobicoke General Hospital Patient Tower
Black & McDonald was responsible for supply, install, testing and commissioning of the entire electrical scope of work this important community healthcare institution…

Women’s College Hospital Redevelopment
The Women’s College Hospital Redevelopment involved construction of a new medical tower. Black & McDonald was the Design-Build, Integrated Electrical-Mechanical subcontractor on the…
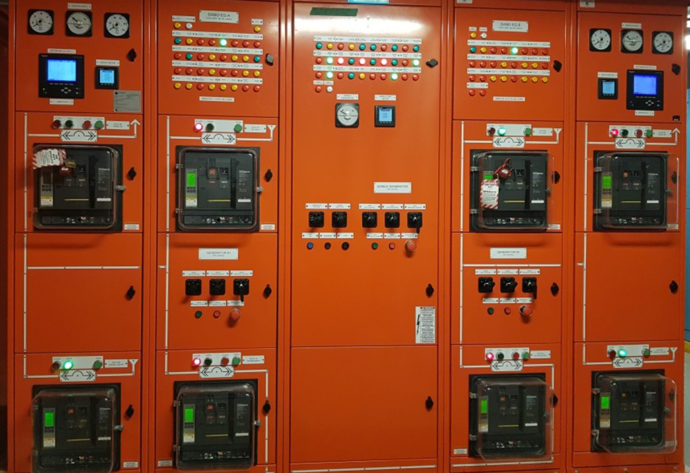
TCCCC Infrastructure and Resiliency Upgrades
The project consists of electrical and mechanical infrastructure upgrades to the TCCCC including architectural/structural works. Black & McDonald was the general contractor.
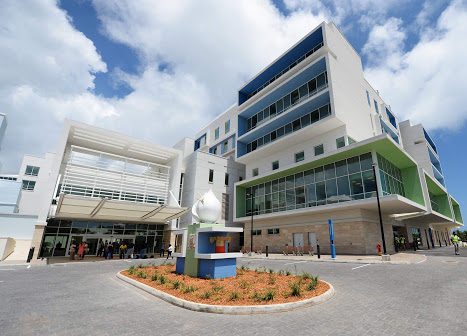
King Edward Memorial Hospital Re-Development
Black & McDonald was the contractor for the mechanical and electrical installations for the new Acute Care Wing of KEMH and provides facilities…

University of Toronto Infrastructure Upgrades
Black & McDonald undertook a major HVAC infrastructure upgrade at the Lash Miller building across its six floors to realize drastic energy savings…
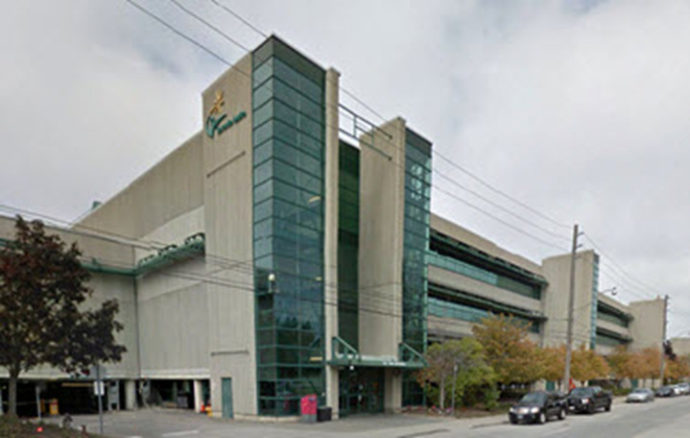
Toronto Hydro Data Centre
The Toronto Hydro project involved the conversion of existing warehouse space for the construction of an updated data centre and a state-of-the-art control…
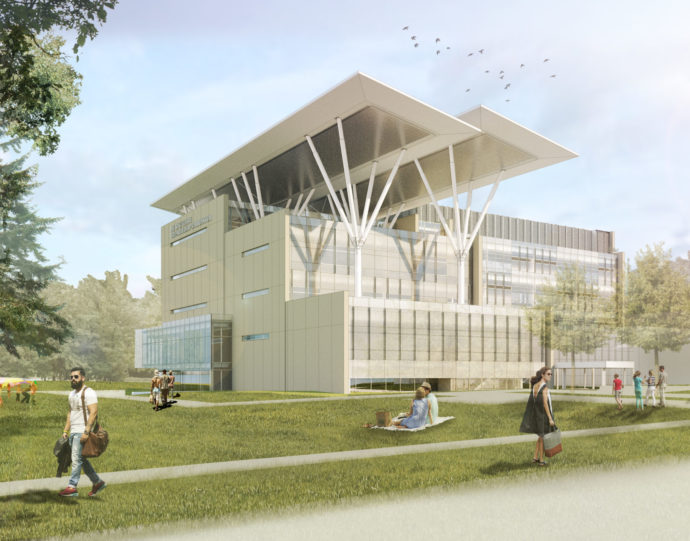
Mohawk College Joyce Centre
Black & McDonald completed all electrical & communications works for the Mohawk College’s Joyce Centre for Partnership & Innovation which is a 96,000…
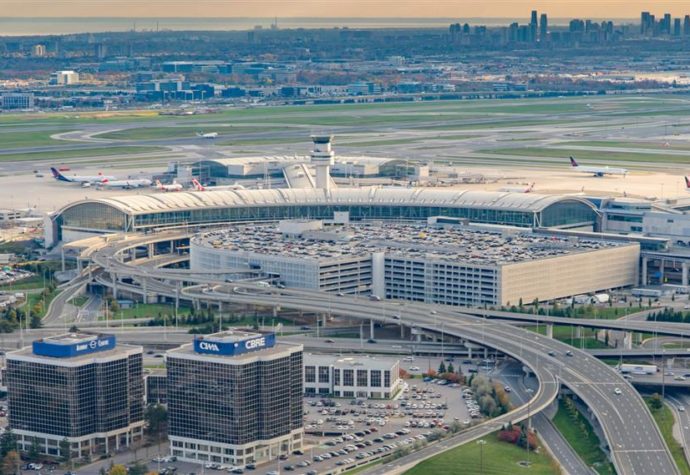
GTAA Next Generation Antenna Systems
Black & McDonald was hired as the construction partner by Ericsson Canada to design and build Next Generation Distributed Antenna Systems (DAS) at…
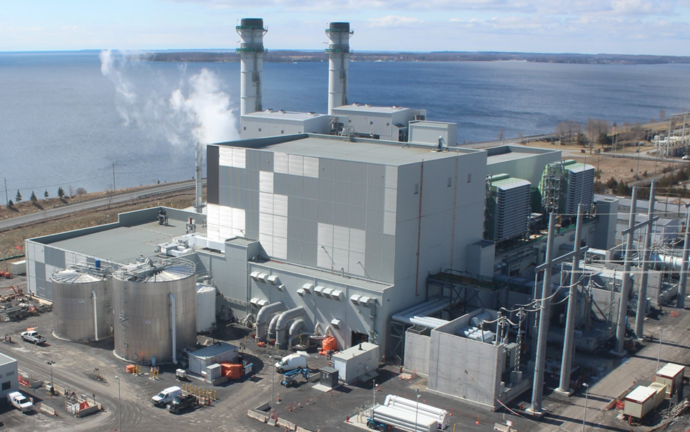
TransCanada Napanee Generating Station
Black & McDonald was engaged by TransCanada to perform the electrical completion work on all balance of plant electrical power systems associated with…

Government of Ontario Modernization
The ESAP project is a billion dollar P3 DBFOM project that provides modernization of District Energy System (DES) that currently provides heating and…

Zenabis Marijuana Grow Facility
Black & McDonald provided more than 75 personnel for the Phase 2A Supply and Installation of a Grow Room electrical project, and was…

Wisokolamson Wind Farm
Black & McDonald took on the full design and construction responsibilities for the construction of these wind power generators and electricity infrastructure.

Voisey’s Bay Nickel Mine Construction
Black & McDonald provided expertise to expand Vale's living accommodations for the new mine. B&M build the site, right through to its completion.
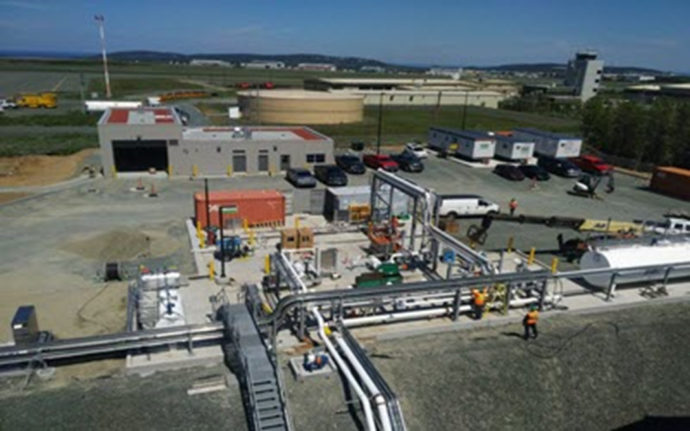
St. John’s Airport Fuel Loading System
Black & McDonald was selected as the general contractor with subcontractors for civil work, building construction and coatings to complete the installation of…

St. John’s Airport Generator Replacement
Black & McDonald completed the installation of two new generators at the Field Electrical Centre located at the airport. The project was scheduled…

Pugwash Central Water Supply System
Black & McDonald was contracted to build a centralized water treatment plant, as well as an associated reservoir and distribution system for the…

Nova Scotia Power Hurricane Recovery
Black & McDonald sent 15 people, including seven line trucks and one support truck to assist with the Hurricane Dorian relief efforts.

Nova Scotia Power Customer Operations Centre
Black & McDonald provided its expertise to Nova Scotia Power for fixing the issues with its Customer Operations Centre.
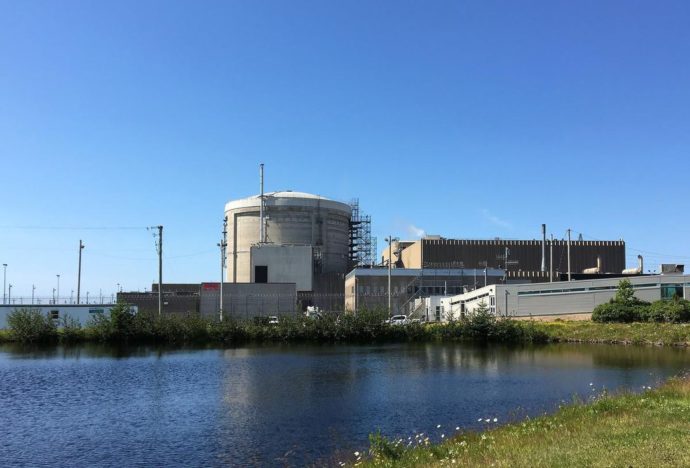
NB Power Point Lepreau Nuclear Station
Black & McDonald partnered with NB Power to install its fibre cable throughout the Point Lepreau site.
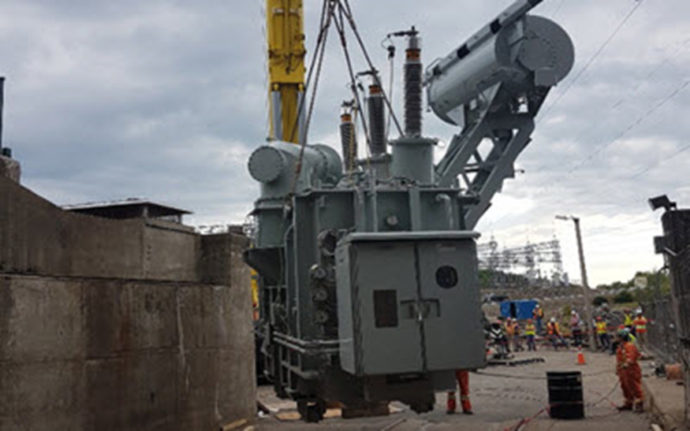
NB Power Beechwood Hydro Station
Black & McDonald was selected to coordinate, plan, and execute the replacement of a 40 MW transformer, located in the Beechwood Hydroelectric Station.

Nalcor Muskrat Falls Accommodations
Black & McDonald installed eight additional accommodation dorms at the Muskrat Falls Generating Station construction site, resulting in an additional 480 rooms to…

Churchill Falls Hydro Station Modernization
Black & McDonald completed the installation and retrofit of all controls pertaining to unit A3 Hydro Turbine for CFLCo (Nalcor).

Kloosterboer Cold Storage Expansion
Black & McDonald presented a professional plan to conduct the replacement of an old system at Kloosterboer.
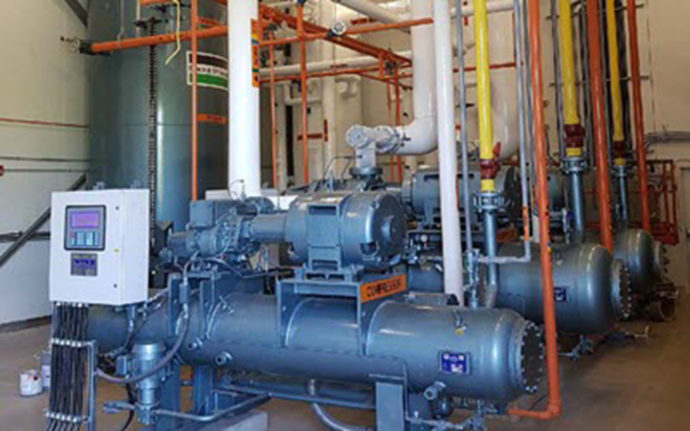
Kelcold Cold Storage Refrigeration System
Black & McDonald assisted Kelcold of Moncton to overhaul its refrigeration system and implemented the project right from design to build.
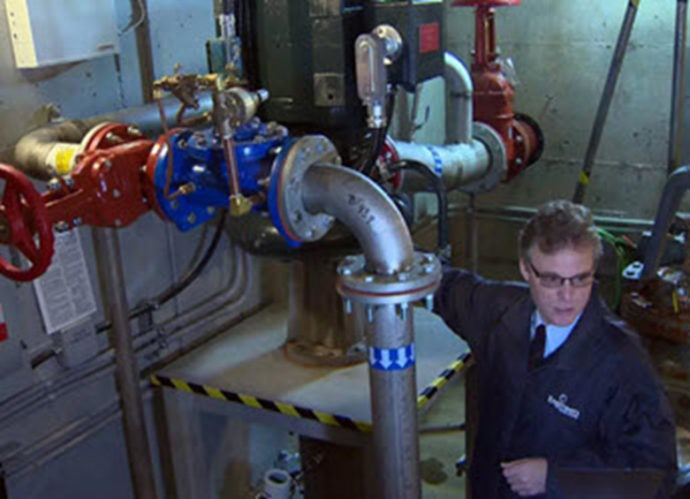
Halifax Water Filter Rehabilitation
Canada’s first regulated water utility, Halifax Water put its trust in Black & McDonald to provide the mechanical expertise needed to ensure the…

Halifax Fort Needham Upgrade
As a community landmark for visitors and locals alike, this project’s completion and success reinforced Black & McDonald’s reputation as reliable and respectful…
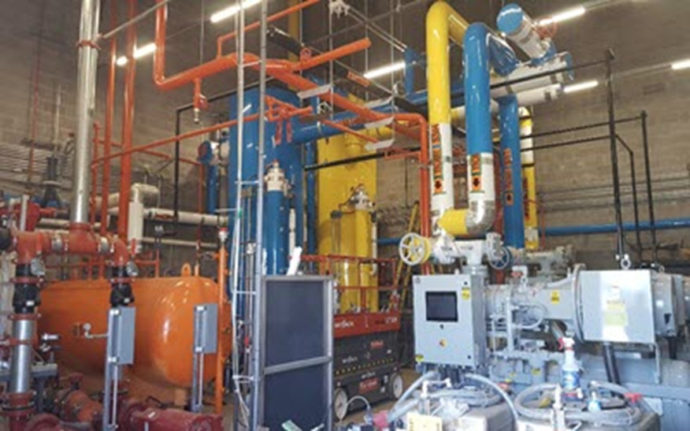
Gordon Cold Storage Expansion
With an extensive expansion plan, GFS called on Republic Refrigeration Inc. to partner with Black & McDonald to develop an innovative and state-of-the…
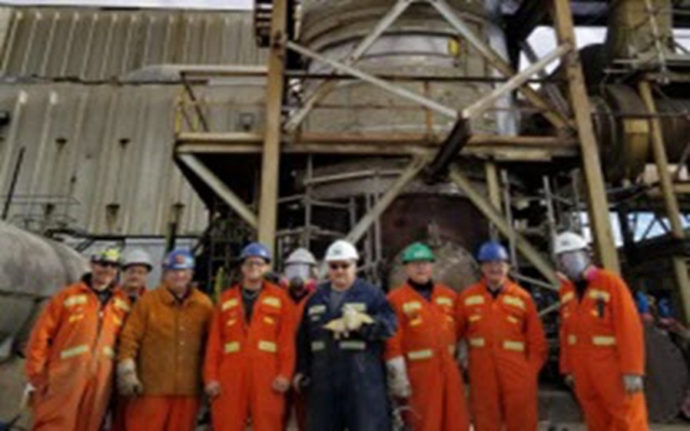
Glencore Canada Acid Plant Shutdown
Based on the past experience, Glencore’s Brunswick Smelter chose Black & McDonald to provide the necessary workers to perform repair of the Acid…

Dalhousie University Energy Transfer Project
Black & McDonald provided its expertise to Dalhousie University with refurbishment of its HVAC system at the campus in Truro, including replacing its…
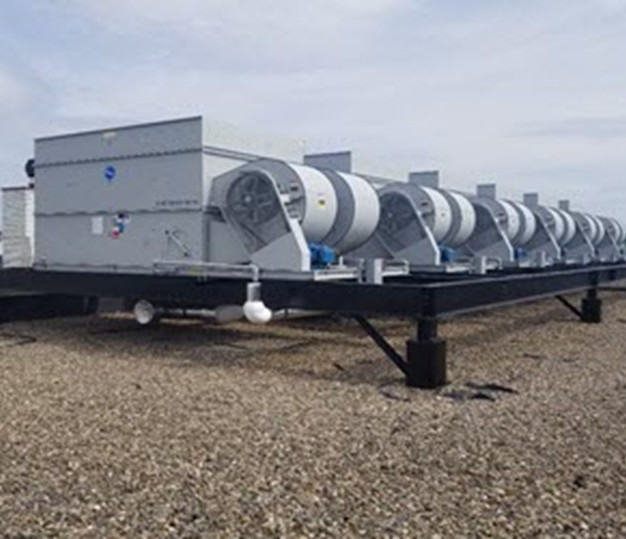
Cushman & Wakefield Cooling Towers
Black & McDonald successfully bid on this project to meet a tight time deadline, complex logistics including the continual operation of the chiller…
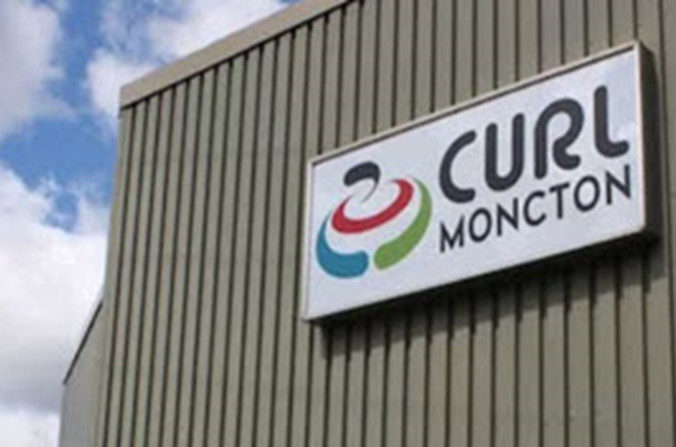
Curl Moncton Icehouse Expansion
When Curl Moncton embarked on an expansion of its facilities in 2018, the organization hired Black & McDonald to provide electrical, plumbing and…

Cavendish Farms Install & Upgrade
Black & McDonald assisted Cavendish Farms to update its HVAC and refrigeration systems by providing expetise in mechanical design and engineering.
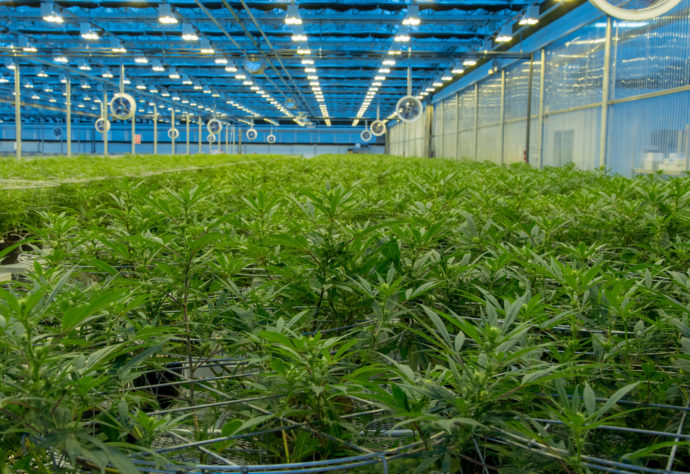
Canopy Growth Mechanical Piping
When Canopy Growth needed to undertake an expansion to its operations in St. John’s, Black & McDonald led the installation of the mechanical…
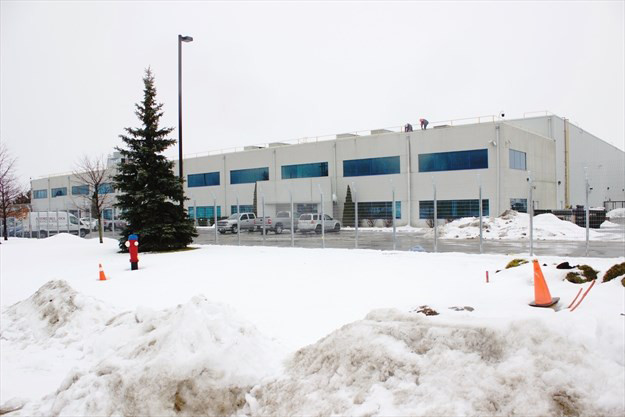
MedReleaf Medical Marijuana Facility
Transformation of MedReleaf's 250,000 sf industrial production facility into a world class medical marijuana growing facility and research lab including retrofitting plumbing, electrical,…
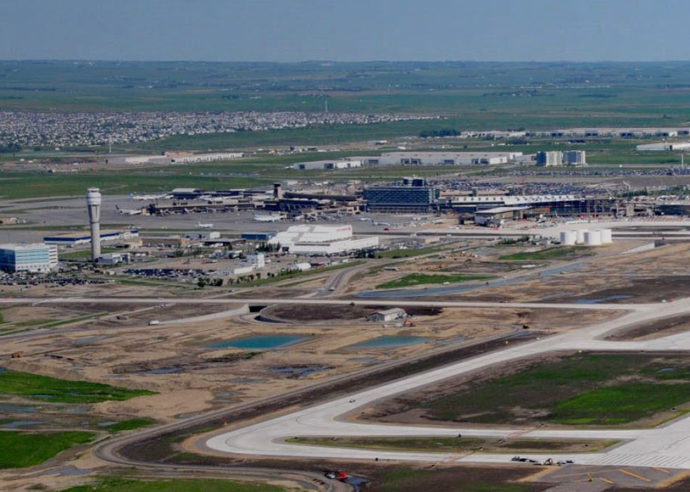
Calgary Airport Runway Development
Black & McDonald provided installation, testing and commissioning of inset lighting, apron lighting, floodlighting, approach systems, and all associated conduit and cable works…
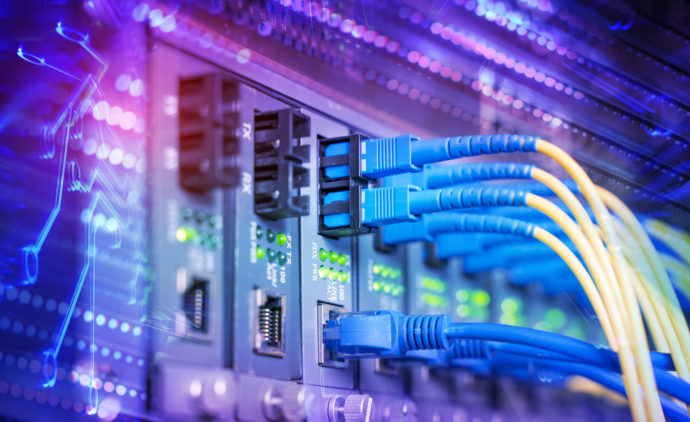
Bell Canada Network POD Installation
Black & McDonald successfully assisted Bell Aliant to expand its networking facility in the historicToll Building at the north end of Halifax.
Get In Touch
Join Our Team
You believe that if something’s worth doing, it’s worth doing right. That solutions should be made to last. That being part of a team means working not just for oneself but for one another. That’s how we operate too.
